引入精益管理方式,需要提前做到这九点
原创-
2022-02-22 13:25:24
-
1498
随着精益管理方式掀起的学习热潮,许多企业也纷纷投身精益管理方式的转型中。不少企业通过精益管理方式解决了诸多困扰自身问题,实现了增产增效,建立了适合各自企业的精益管理体系,但也有许多不成功的探索。究其原因,通常都是因为没有将精益管理的内核与企业自身发展相结合。仅仅将精益管理理解为:“5s、看板、安东(Andon)系统、JIT (Just In Time)、平准化”等一系列管理工具,从而将这些工具生搬硬套的应用到各自企业的日常管理中。
企业想要引入精益管理方式,需要首先理解精益管理的概念。并明确它的核心是:降本增效,减少浪费,最终提升企业效益。总的来说,在企业使用精益管理方式时,我们先要理解并认同以下九点关于精益管理的基础,从而帮助精益管理模式在企业得到更多的认同,最终实现更好的落地。
精益管理需要有一个长期的显化过程,在企业实施精益管理的前期或中期,企业的盈利或者效益并没有明显的增长,甚至有可能出现短期停滞。但要实现精益生产,企业就需要将精益管理设定为优先于企业短期增长的目标。
企业的流程需要持续的迭代、改善,以适应不断变化的市场大环境,通过精益管理方式,引导管理者更加重视流程,通过建立循环、不间断的流程,企业的生产和管理工作会高速的运转起来,最大可能将生产过程中空闲等待或等候配合其他工作的时间压缩到最小。
精益管理思想认为,公司的浪费无处不在,生产过程中就会产生有形和无形的浪费,这些可以通过精益管理模式来避免,认真分析顾客需求,通过顾客的需求,调配生产各个环节,最终供应与客户需求相符数量的产品。事实上,在软件研发过程中,浪费也随处可见,甚至更为惊人,这些浪费主要体现在:
1. 额外的功能特性设置
传统的软件开发过程中,会有意无意地制造了大量人们不需要的功能,而这些过多的功能特性会让系统变得冗杂,也会增加团队的开销。
2. 存货
传统制造业中的七大浪费之一就是“存货”,这也存在于软件开发中,常见的现象是已完成的功能不得不等待很长一段时间才会被测试,而被测试了的功能会等待相当长一段时间才会被客户验收,这些通通都可以算是软件开发过程中的存货,它们是软件开发过程中的第二大的浪费。
3. 过度处理
过度处理不仅存在于软件需求中,还存在于代码中。不少程序员或者研发团队,会在代码中去做很多“预防性”工作,以应对可能会发生的问题。这种做法一方面增加了程序不必要的复杂性,另外一方面如果“可能的”情况永远没有发生,这些代码就成为了一种浪费。
4. 信息传递
开发团队经常面临的境地是很难找到客户进行需求沟通和确认,或者不得不花费很多时间和精力去寻找各种需要的信息,团队用在寻找信息上面的时间,并不直接创造软件的价值,所以也可以归为一种浪费。
5. 软件缺陷
在软件开发过程中,发现Bug、报告Bug、定位Bug、修复Bug、验证Bug等都要投入人力、物力和时间,这也是软件开发过程中一种无形中的浪费。
6. 等待
一款软件从研发到交付,中间产生的或长或短的等待时间。无论是客户的等待,还是开发团队内部的互相等待,都是没有价值的事情。与此同时,等待也会推迟问题的暴露和解决时间,不可避免的造成浪费。
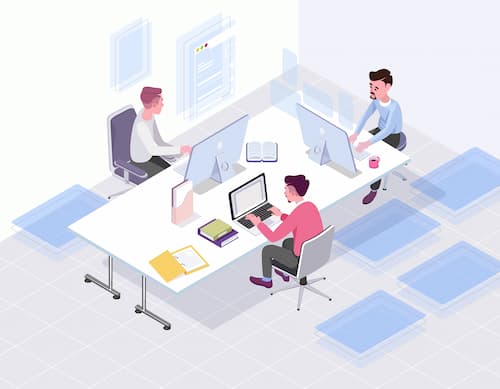
四、建立立即暂停以解决问题的魄力
从一开始就重视品质管理的文化。在丰田公司的生产线上,有一套叫做 Andon 系统(安东系统)的停线装置,任何一个工人都可以因为品质、安全等问题,立即停止生产线的运行。 精益管理认为,建立立即暂停以解决问题机制,这样能够保证问题发现即停止,保证产品品质。
精益管理方式鼓励各部门将工作中的常规工作,通过制成“标准化工作指导书”等方式进行分享和复制,并结合日常的工作不断优化,改善,以此来提高工作效率,更有利于为公司和部门快速培养新人。
可视化的目的是告诉员工应关注什么,比如安全、质量、效率、成本、员工、文化等等。实际上可呈现的内容并不止于此,企业和管理者可将任何生产管理中重要的信息。通过电子看板或白板进行可视化展示。这样可用使公司倡导的理念、工作目标、工作要求等一系列问题,每天清晰的呈现。同时也可使用A3资料管理的方法。A3资料是丰田公司在精益管理中普遍使用的一个标准方法和核心沟通工具。具体实施方法时:用一张A3纸总结一个问题,将问题解决的8个步骤(明确问题、分解问题、设定目标、把握真相、制定对策、实施、评价结果和过程、巩固成果)进行归纳总结,将所需要解决的问题做成的A3资料,通过领导和团队的讨论,快速找出解决方案。
在企业实施精益管理,不能盲目推进,需要培养能够接受并认可精益管理理念的团队与个人,使得精益管理的价值观得到有效推行。并通过定期的学习和培训不断强化,教会员工如何以精益思维方式完成团队间高效合作,与公司共同实现经营目标。
大野耐一曾经提出“没有问题才是最大的问题”。在丰田公司的精益管理中,PDCA是一个持续滚动不断向上的循环。打破现状,持续改善,制定目标,达到目标,如果成果与目标有偏差,就要检讨问题所在,通过PDCA循环管理,帮助公司不断探索上升空间。
丰田公司的精益管理模式,来自于其企业价值观和管理哲学,丰田公司对人的基本想法是“所谓的尊重人性,就是让人不做无效的工作,提高人的价值”。精益管理模式也提倡“挑战精神、不断改善、团队协作和尊重他人”的人文精神。因此贯彻落实精益管理方式需要企业将“尊重个人、以人为本”的精神作为主导信念,发挥每一位员工的能力和个人价值。
综上所述,学习和落实精益管理思维,企业和团队需要提前做好功课,不仅在工具和管理管理方式上精益化,也需要在公司的价值观层面,完成精益思维的转型。构建精益文化和精益管理体系。为公司的精益化管理夯实基础、做足准备。