从科学管理到丰田生产模式,精益是如何产生的?
回帖数
1
阅读数
576
发表时间
2024-04-07 09:24:28
一、科学管理理论:建立科学化的、标准化的管理方法
1878年,22岁的弗雷德里克·温斯洛·泰勒进入米德维尔钢铁公司做机械工人,当时米德维尔内部早已实行了计件工资制。原本能够调动起员工积极性的计件工资制,却因为管理者的一些“操作”让整体效果适得其反: 在工人提高了工件的产量之后,管理者却调低了计件的单价。这样,即使是产量极高的工人,他们的最终工资也并不理想。
管理者的这一行为引起了工人们的不满,他们对此做出了“无声”的抗议:很快,管理者们发现,工人每日的产出工件数会在一个较低的区间内上下浮动,且这一现象不只出现在一位工人的身上,而是出现在工厂内所有工人的身上。进入工厂后的泰勒也发现了这一问题,原来工人们为了表达对管理者压低工件单价的不满,自行商定了一个能够轻松完成但又不会被解雇的工件数。同时,工人们还认为如果自己努力工作,那么其他人的工作机会就会减少。
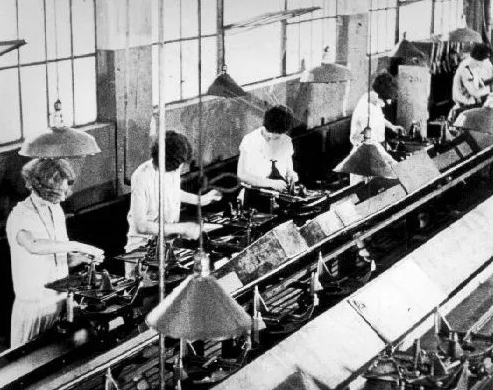
这里借用陈春花老师的一个观点,“泰勒明确提出,管理要解决的就是,如何在有限的时间里获取最大程度的产出,也就是如何使劳动生产率最大化的问题。”
尽管当时的工人对泰勒推行的“科学管理”嗤之以鼻,但正是由于泰勒的贡献,让工厂管理开始从经验管理过渡到科学管理阶段。
二、大规模生产方式:让汽车走进千家万户
在科学管理理论的影响下,第三次创办公司的福特总结了前几次失败的教训,花了大量精力研究市场需求, 更加关注劳动生产率的最大化。这次的创业非常成功,福特公司接连打造出了成本低、质量高的A型及N型车。投入市场后,这两款车的高销量给了福特很大自信。
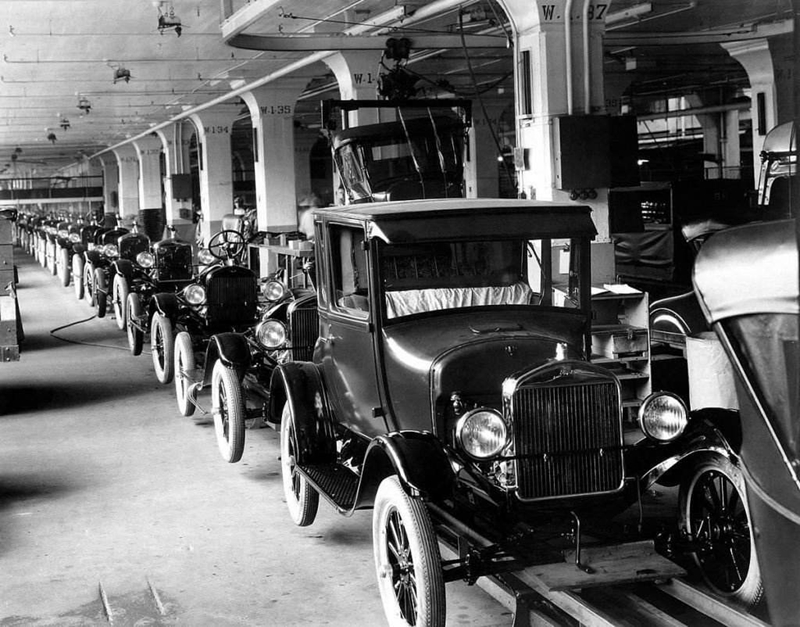
为了在短时间内有更低成本、更高回报的产出,福特致力于寻找更优的汽车生产方式。一次在观察屠宰场工序的时候,福特意外得到灵感,开始着手打造世界上第一条汽车流水线。在这一条流水线上,福特开始打造T型车。首先将T型车的装配过程拆成了84个不同的步骤,让流水线上的每一个人都专门做其中的一个环节。这样,整条流水线的流程走完之后,一辆汽车就组装好了。流水线的应用让汽车装配时间由12小时缩短至90分钟,同样的,T型车的零售价格在短期内从850美元降到300美元。到20世纪20年代,福特公司的汽车已经占据了美国60%的市场份额。
三、丰田生产方式:减少浪费的拉动式生产系统
为了拯救丰田已濒临崩溃的生产过程,时任丰田副社长的大野耐一去福特工厂实地参观福特的生产模式。在实际引入福特的流水线生产方式并运行了一段时间后,大野耐一发现,福特的这种生产虽然快速、方便,但会出现库存过多,质量无法及时检测等问题,产生了不同程度的浪费。随后,受到超市按需进货的方式启发,大野耐一决定创建一个“ 消除浪费、持续改善”的精益生产方式。
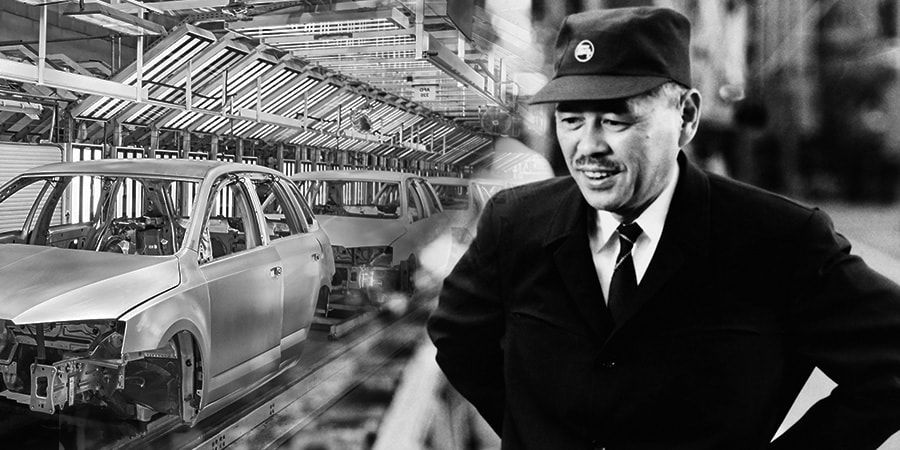
在福特生产模式的基础上,大野耐一提出了“准时生产(JIT)”, 决定控制库存,力求达到“零库存”。准时制的基本思想是“只在需要的时候,按需要的量,生产所需的产品”。准时生产通过看板管理进行“后拉式”带动生产,实现清晰、有序的生产管理,拉动价值流动,使在制品、库存减少,从而有效地提高了生产效率。
除此之外,大野耐一针对丰田生产过程中的其他问题,提出了相应的解决方案,在不断优化、改进后,最终找到了一套适合丰田自身的标准化流程,逐步形成了以人为本、全员参与、追求质量,并能够在过程持续改善的精益生产方法。
1970年后,随着市场环境的变化,以美国为代表的大批量生产模式的短板逐渐暴露,丰田的精益生产方式开始进入人们的视野。
1996年,美国麻省理工学院的Daniel T.Jones教授出版《精益思想》一书,从理论的高度归纳了精益生产中所包含的新的管理思维,并将精益方式扩大到制造业以外的领域。精益生产方法不再局限于生产领域,促使各领域管理人员重新思考企业流程,消灭浪费,提升价值。
2024-04-07 09:24:56 敏捷开发 最后编辑
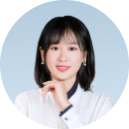
联系人
刘璐/高级客户经理

电话(微信)
18562550650

QQ号码
2845263372

联系邮箱
liulu@chandao.com
